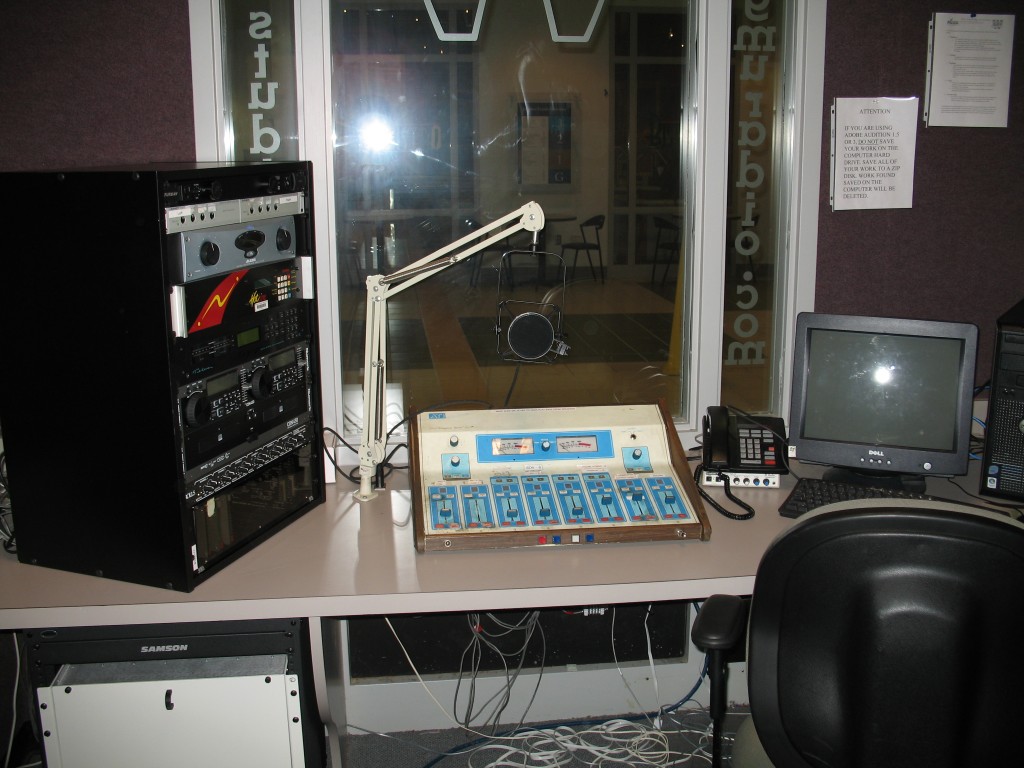
Our ancient metal rack has been replaced by two racks, a particle board rack on the table and a brand new metal rack underneath.
After completing the upgrade of the Practice Studio, I am turning my attention to upgrading WGMU Radio’s Production Studio on the ground floor of the Johnson Center. I originally wanted to complete this project over the summer, but our Business Manager suddenly retired in April, and I inherited his duties due to my previous stint as Business Manager back in 2001. Needless to say, absorbing an additional 0.5 FTE worth of work is tough.
The console in the Production Studio, ATI Vanguard, is a virtual twin of the one that was in the practice studio, except that it is slightly newer (early 80’s vintage) and has a set of four cart machine controls on the front. At around 30 years old, this piece of equipment is older than most students that use it. I can’t fault the console’s durability, but it is functionally obsolete, so it has to go. Luckily, the same employee of the Associate Press who donated equipment for our Practice Studio also donated a second Logitek AE-32 Audio Engine and Remora control surface for use in the Production Studio.
Overall, the Production Studio is a mess. Whoever set it up initially knew what they were doing. Unfortunately, all their handwritten labels on the 66 block faded away a long time ago and numerous people since then have installed various unlabeled and undocumented hacks. My favorite is the “poor man’s mix-minus bus”. Since the Vanguard doesn’t have a min-minus bus installed standard, someone kind of made one by tapping into the Mic 1 pre-amp output and connecting it to the Telos Zephyr ISDN codec. This does work although it drops the output of Mic 1, which makes it more difficult to balance it with Mic 2.
Other issues include both mics wired out of phase, the 3.5mm computer connection swaps the left and right channel and the shield pin isn’t connected in many XLR jacks – probably a clumsy attempt to fix a ground loop hum issue.
The first step in the studio upgrade is to install all the equipment we purchased over the summer into the equipment racks. Originally, we tried to install the equipment in our ancient gray metal rack, but after Rodger Smith asked that we move the Comrex Hotline to the Production Studio in order to handle Women’s Basketball broadcasts, we didn’t have enough space (even after ditching the old Technics compact cassette deck).
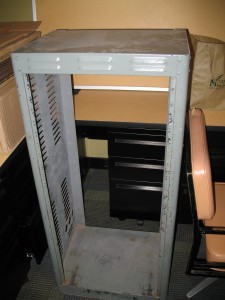
Our ancient gray metal rack.
That is just as well since we had trouble screwing in the equipment into our ancient gray metal rack because the threads were rusted. Also, true story, back when it was new (World War II?), the rack was actually black and when it begun to rust, someone decided to paint it gray. Why? I assume that gray paint was on sale at the time. Repainting would have been perfectly OK if they sanded off the rust first and smoothed out the paint, but they just sprayed over the mess and called it a day. That is what gives the rack its wonderful mottled appearance.
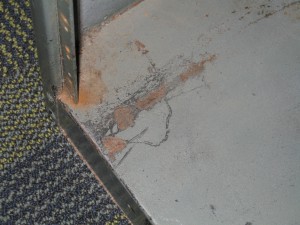
Rust collecting at the bottom of our ancient gray metal rack.
I made the decision to use two medium size racks instead of one gigantic rack, primarily because I didn’t think the table could handle the weight, and because it would be tough to reach the equipment at the top of the rack from a sitting position.
The upper rack is the particle board rack from the Practice Studio. It was too big for the Practice Studio, but just right for the Production Studio. I gave it a good cleaning and added felt strips on the bottom so it can slide around on the desk without scraping it up. The equipment in the upper rack is (from top to bottom): Furman PL-8 C Power Conditioner*, Aphex Distribution Amp (which I would have removed if I actually knew what was patched through it), Alesis RS300 Amplifier, Comrex Hotline POTS Codec, Telos Zephyr ISDN Codec, Numark CDN450 Dual CD Player*, Rolls RA62c Headphone Amplifier* and Benchmark System 1000.
* New Equipment
The lower rack is a brand-new Samson SRK12 rack. The Samson is a great rack for the money. It is completely steel, includes casters and has both US and European threads. The gauge of the steel isn’t as thick as our ancient gray metal rack, but not bad overall. I put the Logitek AE-32 Audio Engine and Benchmark PS202 Power Supply in the lower rack since neither piece of equipment has any front controls.